A pre-assembled harvest module is being shipped aboard the liner “Condor Bilbao” from Lerwick in Shetland via Antwerp and on to Puerto Montt in Chile where it is scheduled to arrive 14 January, in the new year.
The harvest plant was exported by AquaShip to Gripship Chile for use on 1800m3 wellboat, the “Grip Pacific”, which is on long-term charter to salmon farming company, Blumar Seafoods.
“It’s an interesting concept,” Alan Bourhill, General Manager at AquaShip UK explains. “It’s a harvest module. One of the things we specialise in is on site harvesting using deck mounted harvest equipment – harvesting into wells using small converted wellboats.”
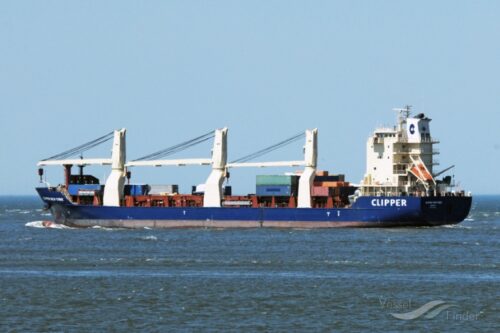
“The key innovation is that the system that we have designed and built allows a conventional wellboat to be turned into a ‘utility wellboat’ enabling the harvesting of fish at the quayside.”
Bourhill continues, “Existing technology is either or i.e. transporting live fish onto a shore based harvest system adjoining a primary processing factory or a harvesting at the cage-side using a dedicated harvesting vessel.”
The harvest module dimensions are 12m x 6.8m x 5m with a weight of 25.8 tonnes. While the system has 14 lanes capable of harvesting up to 14,000 fish (or 84 tonnes) per hour.
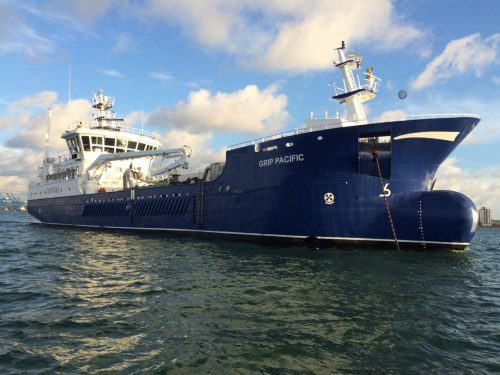
“The fantastic fact is that it was fabricated from flat steel and aluminium in 12 weeks – the whole fabrication was undertaken here in Shetland.”
The module is particularly suited to Chile, Bourhill explains. “They have a lot of production sites, which are several days away from more centralised processing facilities. So you would go out and collect live harvest ready fish from a pen and steam live as you would delivering live harvest fish into a shore based killing system.”
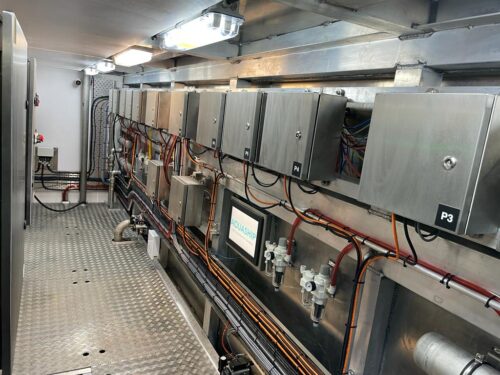
Operation
Once installed, the system in many ways operates in the same manner as a normal harvest line. Specially designed fish pumps transfers fish from the vessels hold, to the harvest system. The water separator removes all the water sucked up from the hold by the pump and returns it back to the hold. The swim-tank and the design of the counter current water flow in it encourages the fish to swim into the pneumatic stun and bleed machines.
Computer controlled tailgates open and close in sync with the pneumatic stun and bleed machines to only allow single fish to enter the stun and bleed machines. The pneumatic stun-bleed machines. These air-powered machines by holding each fish in turn; delivering a non-recoverable 200 newton (N) hammer blow to the head immediately above the brain followed by knife, driven by a second pneumatic impact cylinder, that cuts the fish from below at the isthmus, to bleed out.
“The force we utilise in our system exceeds the established level required to ensure an efficient stun without recovery.”
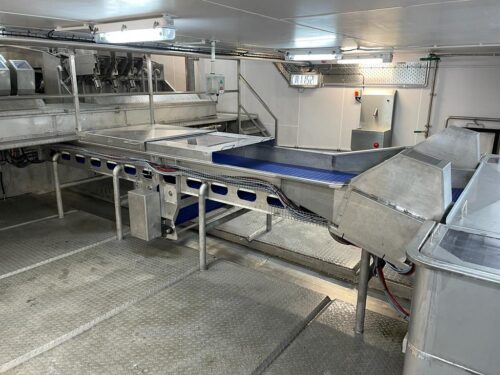
On to the quayside
After the primary stunning and bleeding process fish are transported along stainless-steel channels and/or speed-controlled conveyor belts into one of two 34m3 buffer tanks past trained operatives who check stunning efficacy and bleeding accuracy. Secondary stunning machines (percussive or electric) are in place to handle insufficiently stunned fish or fish that have bypassed the primary system.
The two buffer tanks are filled up and emptied in turn and are fed by the vessels refrigerated sea-water system. This system will initially cool the sea-water present in the tanks to 0.5oC in and continue to cool the fish until immediately prior to discharge. As the first step in a temperature controlled supply chain the use chilled water is a solely a quality focused measure.
Finally, the buffer tanks are emptied in turn into tankers on the quayside for delivery to the factory.
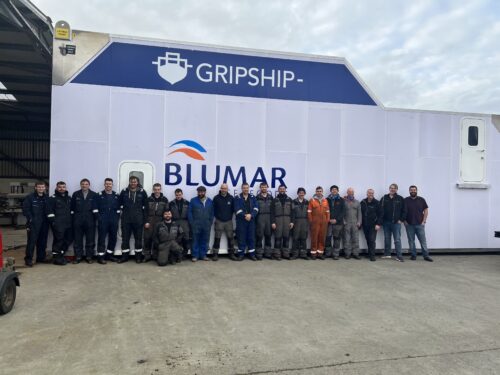